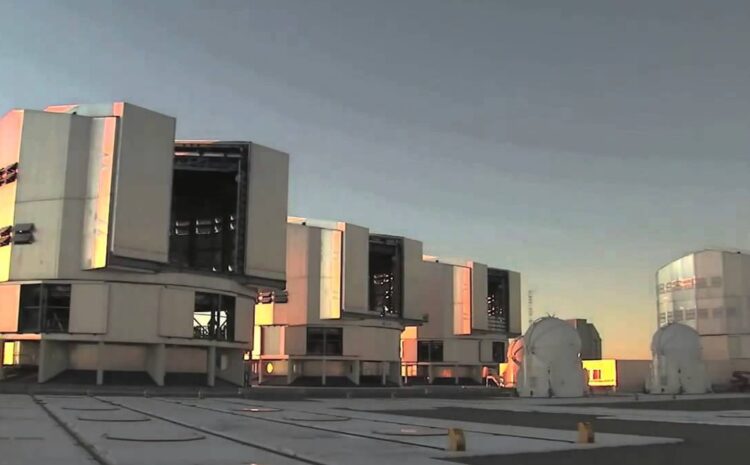
Fabrican en Galicia un coche eléctrico más ligero y que se puede reciclar
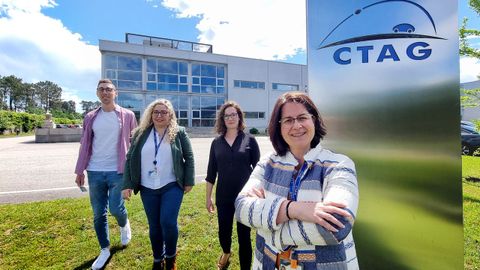
Raquel Ledo, en primer plano, es coordinadora del proyecto Alma por el coche eléctrico más ligero.
La carrocería es de acero de baja densidad y poliéster reforzado con fibra de vidrio. Emplean ultrasonidos para conocer el estado de las piezas y reutilizarlas
El peso de la electrificación es un terreno por explorar. La diferencia de carga entre un vehículo de combustión y su homólogo enchufable es considerable. Un Renault Mégane de gasolina, por ejemplo, pesa 1.306 kilos. El mismo modelo, con una batería pequeña, llega a 1.590 kilos. Y el de mayor autonomía alcanza los 1.710. El Centro Tecnolóxico da Automoción de Galicia (CTAG) lidera Alma, un proyecto europeo para mejorar la autonomía de los eléctricos mediante la reducción del peso de su estructura. Ya han conseguido adelgazarla en un 26 % y aumentar su autonomía. Trabajan sobre un Ford Mondeo, ya que este fabricante respalda el desarrollo junto con el gigante ArcelorMittal y otros siete socios de cuatro países.
Alma está centrado en el chasis del vehículo, explica Raquel Ledo, coordinadora de este proyecto dotado de 5,2 millones de euros y que se extenderá hasta enero del 2024. En esta última fase, lo fabricarán. No proyectan las partes interiores, ni neumáticos, ni motores. «El objetivo es aligerar su estructura. Los eléctricos son mucho más pesados por el tamaño de las baterías que incorporan, pero también por todo el material que se emplea para protegerlas», precisa Ledo. Reforzar el dispositivo que genera energía es otra de las principales diferencias de peso que existen con respecto a un coche de gasolina o diésel, por la respuesta que pueden tener estos sistemas de ion de litio en caso de accidente. La más temida es que se incendie. El otro espacio hiperprotegido, que requiere más carga, es el habitáculo del piloto y sus acompañantes.
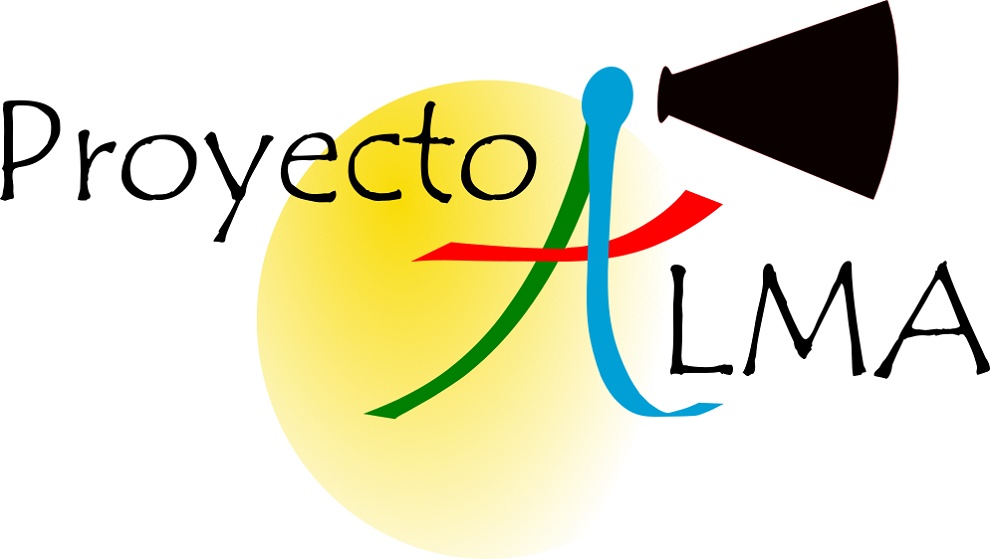
Diseño más ligero
El proyecto se apoya sobre dos pilares claves para alcanzar el propósito de reducir en un 45 % la carga de un vehículo eléctrico tradicional: diseño y materiales. Sobre el primero de ellos, Raquel Ledo indica que han suprimido todas las piezas de las que se podría prescindir. «Donde había tres o cuatro compartimentos, lo diseñamos con tan solo uno. Por ejemplo, en la zonas de las puertas. Entre la delantera y la trasera, la unión que existe es el ensamble de muchas piezas. Lo hemos reducido a una». En esta fase, también prestan atención a aquellas partes que precisan mayor protección. «En un choque lateral, es fundamental conseguir que la puerta no se meta hacia adentro y evitar que toque la batería».
Materiales empleados para un coche eléctrico más ligero.
Por otro lado, el proyecto que desarrollan en O Porriño emplea materiales más ligeros, pero igualmente resistentes en la estructura del vehículo. «El diseño cuenta con aceros muy específicos, de baja densidad y de alto límite elástico», señala la coordinadora de Alma. Se trata de metales «de muy altas prestaciones y de menor espesor», pero que se comportan bien. Han diseñado una herramienta de análisis de ciclo de vida que permite conocer qué material es oportuno en cada parte del coche.

El otro de los componentes innovadores es un composite, un poliéster reforzado con fibra de vidrio. Su uso recuerda a la industria naval o la aeronáutica. «No tiene el mismo comportamiento que los aceros, pero hay distintas zonas del vehículo en las que es adecuado. Por ejemplo, lo usaremos como tapa de la batería o en elementos abrientes, como el maletero», apunta Raquel Ledo, que precisa que no es un material «de uso masivo».
Alma es un proyecto de innovación, «pero cercano a la industria», indica su máxima responsable. De ahí su preocupación porque el precio de los materiales empleados no sea excesivamente caro con respecto a los aluminios que se emplean hoy en día en las cadenas de producción. «No gastaremos más de tres euros por cada kilo que rebajemos», estiman.
Emplean ultrasonidos para conocer el estado de las piezas y reutilizarlas
La normativa actual exige a los fabricantes de la industria de la automoción ir un paso más allá a la hora de concebir un vehículo y deben pensar en qué hacer con el mismo cuando cumpla su vida útil. En base a esto, el proyecto Alma aborda la economía circular desde distintas perspectivas. «Cuanto menos se consuma, mejor» es la principal de las máximas, explica su coordinadora, Raquel Ledo. Emplear tan solo el material necesario para la producción del turismo ayuda a reducir la energía que se precisa en este momento. «Hay que optimizar el vehículo desde la fase de diseño», insiste.
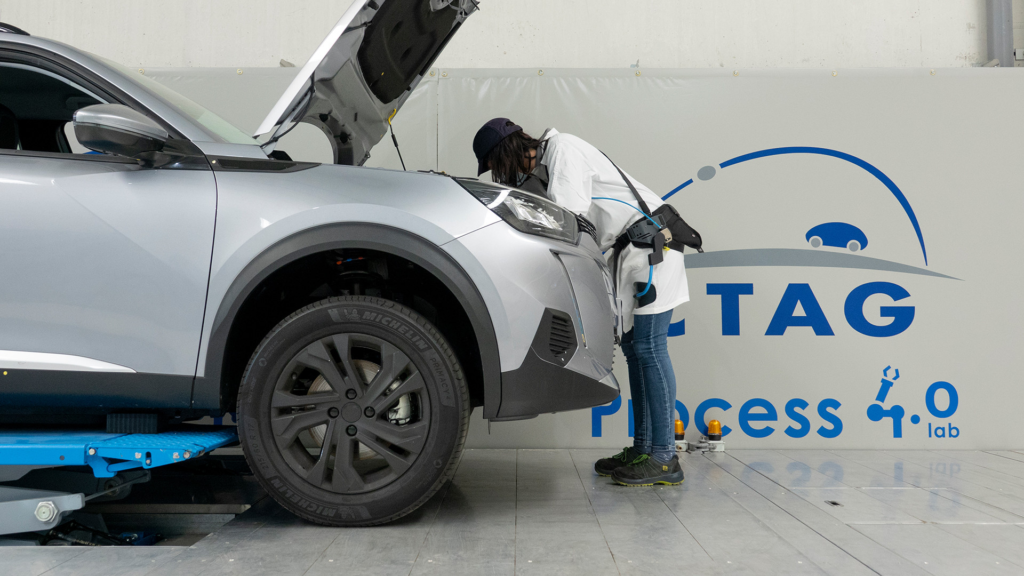
«Pero también pensamos en todo el círculo», continúa. Se refiere a cómo aprovechar el vehículo cuando deje de usarse. «Hasta ahora, uno de los mayores problemas que existían para su reciclaje es que es difícil separar las piezas. Además, es oportuno clasificar aceros por un lado, plásticos y aluminios por otro», indica. En el proyecto Alma han trabajado con adhesivos estructurales, que aguantan fuerzas «impresionantes» y aseguran que las piezas permanezcan unidas. Pero se trata de un material que se desintegra a alta temperatura para que resulte sencillo disgregar la estructura del vehículo.
Además, plantean el empleo de una técnica de ultrasonidos que indica a su ejecutor si una pieza se encuentra en buen estado o no. «Puede ocurrir que haya elementos que hayan sufrido fracturas por dentro y que, a simple vista, se encuentren en buen estado», explica Raquel. «Es como una ecografía», pone como ejemplo. En caso de ser útiles, se aprovecharán para una segunda vida en otro vehículo.
Clica en la imagen y consigue toda la información que precisas
Acceso a la noticia original. coche eléctrico más ligero Fabrican en Galicia un coche eléctrico más ligero y que se puede reciclar (lavozdegalicia.es)